Katrine Vetaas Vedeler, former Director of Responsible Supply Chain for KPMG AS in Norway, tells Future that there is a positive change in how companies are managing their human rights responsibilities, ethical standards, and sustainability credentials throughout the supply chain
While she may have recently left her role at KPMG AS in Norway, Katrine Vetaas Vedeler has been helping companies improve their supply chains – making them more ethical, responsible, and sustainable – for many years. It is a topic she is incredibly passionate about. Why? Because questionable ethics and human rights abuses are still endemic in business supply chains, globally. The issue will undoubtedly continue until all large companies with multiple suppliers perform a rigorous analysis of every link in their supply chains to ensure they are upholding the same high standards throughout.
A key part of Vedeler’s role is to help companies conduct human rights due diligence assessments. The process has several steps. “If you look at how it is defined by The Organisation for Economic Co-operation and Development (OECD), it all starts with governance. So, we provide assistance from the very top of a company,” she says. “If a company is going to build a responsible way of handling its supply chains, we help them assess the extent to which they currently meet best practice and the expectations of international bodies when it comes to human rights.”
From there, Vedeler and her team look at the respective management systems and the kind of policies, procedures and requirement tools a business has in place to manage human rights in the supply chain. “That includes its code of conduct to determine whether it has a human rights policy. We then help them perform a gap analysis,” she says.
For Vedeler’s clients in Norway, it is specifically relevant to look at upcoming legislation because of a new law launched by the Norwegian government called The Transparency Act. “That law will require companies of a certain size to report how they are conducting human rights due diligence. The law is enforced in July next year [2022], so many companies are now wondering what to do about it,” she says. “Norwegian law is completely aligned with the international frameworks on human rights, such as The UN Guiding Principles on Business and Human Rights and The OECD Guidelines for Multinational Enterprises, so those companies that have already started [human rights due diligence], are closer to meeting the expectations.”
The next step is to conduct risk assessments. “We support our clients in finding where they have the highest risks in their supply chain,” says Vedeler. “That’s also very closely linked to international frameworks where you are supposed to try to understand your supply chain, acknowledge where you have risks and then prioritize the risks that have the largest impact in terms of scale, scope and remediability – potential harm to peoples’ human rights.”
That “potential harm” can be manifested in any activities being undertaken by workers within a supply chain. “We try to help [clients] narrow the scope where their responsibilities are through the risk assessment,” says Vedeler. “Then we can help them conduct audits, controls or engagement activities with their suppliers that help them ask, ‘Does our supplier risk harm to people in their supply chain and in their operations?’ We do that by speaking with the supplier’s management team. We also speak with the workers to ask, ‘What’s the situation like?’ in order to understand what kind of risk exposure they are subject to. Then we look at documentation for a selected group of people working with suppliers and triangulate that by looking at policies and procedures. If we find things that are not as they should be according to international or national expectations in their supply chain, then we can help them create an action plan so that they close those gaps.”
“We try to help [clients] prioritize their actions through the risk assessment. Then we can help them conduct audits, controls or engagement activities with their suppliers that help them ask, ‘Does our suppliers risk harm to people in their operations and supply chain?’”
Katrine Vetaas Vedeler
This can frequently be a lengthy process, says Vedeler, if there are serious deviations impacting how a person is able to perform his or her job. And those deviations can cover all manner of ills, from employees working too many hours or not being remunerated a ‘living wage’. There could be indicators of slavery, such as employees being asked to hand over passports or other ID documents to their employer. It could be that they are being harassed or discriminated against or kept from participating in union activities and collective bargaining. It could be that accommodation standards provided by an employer are not acceptable or simply that workers are not being treated with dignity. “There could be grievance mechanisms that workers are not aware of where they can go to speak out about any concerns they might have,” says Vedeler.
Stakeholder power
Not every business has an extensive supply chain, and some sectors differ in terms of their potential exposure to human rights or ethics abuses. So, do manufacturing companies specifically face more of a challenge to ensure their supply chains are responsible, ethical, and sustainable? “We would say that companies that purely provide services may have an easier task perhaps they don’t have so many layers of suppliers. If you produce a product, then you may have many layers of suppliers,” says Vedeler. “It can be harder to map your supply chain. Very often we see that those companies that produce products have the highest risk the further down the supply chain goes, so, it’s necessary to map the supply chain all the way down. But in some industries where they produce products, there has been real progress. For instance, textile manufacturing, which has very complex, long supply chains, has really worked on its responsible supply chains over a number of years.”
“It can be harder to map your supply chain. Often, we see that those companies that produce products have the highest risk further down the supply chain, so, it’s necessary to map the supply chain all the way down, to the raw materials used”
Katrine Vetaas Vedeler
Ultimately, says Vedeler, it makes good business sense to ensure a supply chain is responsible from the outset. “Simply put, a person that doesn’t have to worry about making ends meet, being discriminated against or harassed at work can focus on their job and conduct their tasks well,” she says. “And a company whose workers are well rested and happy can expect to see better quality, faster delivered services – and therefore improvements in incomes.”
Human rights and sustainability regulations are also becoming tougher, at both a country and EU level. Areas that were previously stipulated as guidelines and best practice are now legal requirements for companies. Sanctions against companies that do not manage a responsible supply chain are increasing, but there is also a wider impact not previously felt by big business – stakeholder power. More than ever before, when they deem that a company is not behaving ethically, customers and investors are voting with their feet. The implications of that can be far-reaching for those businesses that do not address their shortcomings. “It may be that consumers turn away from them or investors are not willing to invest in the company,” says Vedeler.
Thankfully, Vedeler is detecting something of a sea-change in how companies now view their human rights responsibilities as well as how they maintain ethics and act sustainably throughout their respective supply chains. “There is an awakening in people in general. Consumers are more aware of the risks out there and our [collective] responsibility for asking questions. The legal landscape is following that awakening among consumers and other stakeholders. The two things are working together. It’s great to see this change in the landscape – it’s a push in the right direction. The younger generation is less patient on this, I would say.”
In addition, many young people will also choose to not work with a company accused of mistreating its people (including, by extension, its suppliers) or the planet, damaging their ability to attract new talent. “This is the way our world is moving,” says Vedeler. “It will be tougher for companies that haven’t worked on their supply chains and tried to understand what kind of risk exposure they have with products or the services they provide. On the positive side for companies, there’s not too much you need to do in order to improve a little bit. But you must start by looking at your supply chain and try to figure out where you have the highest risks, or the most vulnerable workers in the supply chain.”
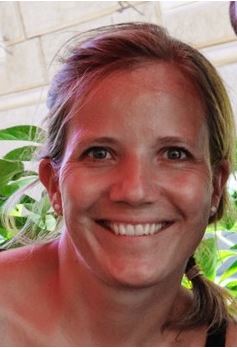